About Topsun Mould Plastic Limited
Founded in 2008, Topsun specialize in plastic injection moulds for automotive, electronic, house appliance and other industrial fields. Located at No. 73, Xingwu Road, WuSha Community, Chang An Town, Dong Guan City, China. We make injection moulds for famous brands such as BMW, STIHL, ABB, and BOSCH. We are a reliable strategic supplier of companies worldwide.
Topsun covers an area of 3000 square meters and has 60 employees. The plant is equipped with advanced tooling machines from Japan, Switherland and Taiwan. The machines enable us to provide high quality moulds to customers all over the world.
We have been working with customers from Europe and USA for over 10 years and are quite familiar with DME and Hasco standards. We look forward to working with potential customers in near future.
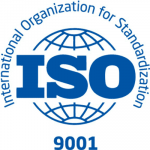
We are an ISO 9001 certified company.
Success Story: Bending Part
Part name: Housing Top
Material: PA66-GF25
Injection system: Mold Master
Cavity: 1X1
Steel: 1.2343ESR
Mold Size: 346X496X520mm
Part of Housing-Top is sucessful case in Topsun Mould. This part flatness is required by 0.5mm and customer had a failure experience in another suplier. When customer asked us for suggestion about this parts, the engineer according to experience and also made the mold flow analysis to supplied best suggestions. Customer was worried about it and we made very detailed plan for customer, we persuade their team to trust us and try it because we had similar part experience. 6 weeks later, we get good samples in T1 and control the flatness is 0.32mm. Of course it is a good news for customer, they are satisfied with our working and very thankful about it, and get the result from customer. Topsun Mould also very happy that customer trusted us and give us a chance to design it.
Success Story: Fresnel Lens
Part Name: Light Lens
Material: PC Lexan 143R-111
Injection system: Mold Master
Cavity: 1X2
Steel: S136
Mold Size: 246X296X320mm
Part of Fresnel Lens is very strict for light. Engineer and designer according to experiences to supplied suggestions for this part, because this part is thick and will caused sink mark, so customer according to our suggestions to optimized the part(don't change the function for this part). We used advanced machine to process and have to meet the optical requirements, after T1 sent the samples to customer to measuring and test, the dimensions and transmission of light are all OK, both of us happily ship the mould to Germany by Air flight.
Success Story: Lens Part
Part Name: 45°ELM 120 Lens
Material: PMMA 80N
Injection system: Cold runner
Cavity: 1X2
Steel: S136
Mold Size: 270X300X305mm
Part of 45°ELM 120 Lens, has 5 exchangeable inserts, the thickness requirement is high, because it will affect transmission of light, so we have to consider more about it. Before we made DFM and 3D design, we have to consider runner, cooling, air venting, etc. Then we used mirrow EDM process and optical polishing. After T2 mould test we get good samples and solved the sink mark and bubble issues.
Success Story: Arc Core-pulling
Part Name: Filettato 1〞1/4 gas
Material: Latigloss 66 H2 G/50
Injection system: Mold Master
Cavity: 1X1
Steel: S136
Mold Size: 596X696X630mm
Part of 45°ELM 120 Lens, has 5 exchangeable inserts, the thickness requirement is high, because it will affect transmission of light, so we have to consider more about it. Before we made DFM and 3D design, we have to consider runner, cooling, air venting, etc. Then we used mirrow EDM process and optical polishing. After T2 mould test we get good samples and solved the sink mark and bubble issues.
Success Story: Screw Part
Part Name: Cooling tube knob
Material: PBT+GF30
Injection system: Cold runner
Cavity: 1X1
Steel: S136
Mold Size: 400X450X471mm
Part of Cooling tube knob is a big screw part(Cooling tube knob), customer had a bad experience of mould core burning and got stuck in another supplier. So when we get this order we analysised old mould structure and found the problem, then we made a new design and updated the mould, after mould assembly we tested for 8 hours, everything is OK and then shipped mould to Japan soon.